Global flight simulator market is sky-rocketing and projected to reach $7.7 billion by 2025 with a CAGR of 5.2% from 2019. With the increasing demand for commercial and military pilots, virtual flight training and certify methods are being adopted for aviation safety assurance and to cut cost for pilot training.
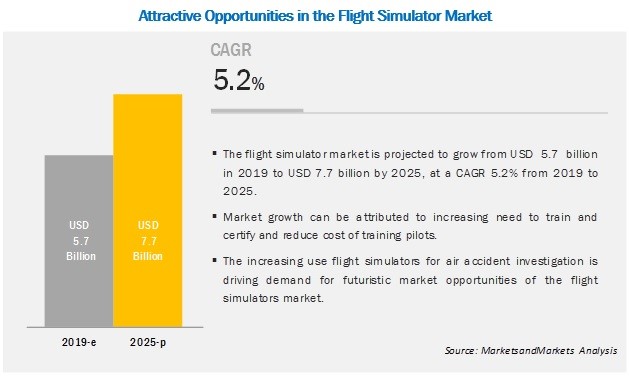
Flight simulators are used to train pilots of commercial aircrafts, military aircrafts, helicopter simulators and Unmanned Aerial Vehicles (UAVs). Growth of the aviation industry is driven by the rise in global air traffic. Rise in demand for aircrafts and pilots acts as a stimulus for the growth of flight simulator market. With flight training simulators, the pilots are trained to handle critical system failure to ensure the success mission execution with prioritized safety. Flight training develops situational awareness to recognize certain conditions to anticipate coming situations. Additionally, pilots use judgement, communication and task prioritization tools during a flight.
Aviate, Navigate, Communicate is the golden rule for pilots
For instance, the pilot-in-command of an aircraft operates within the Instrument Flight Rules (IFR) by relying on the on-board flight instruments and equipment to safely complete the mission. Critical system malfunction is not ideal. However, complete electrical failure can hinder with the navigation operations as well as disrupt the communication system. In such a case, the pilot’s judgement, knowledge and task management skills are vital as it determines the mission outcome. Without the navigation and communication systems, the pilot is required to aviate for a successful completion of the mission. As per the golden rule, pilots should prioritize aviation above navigation and communication.
Flight simulators train pilots to handle dynamic real-life scenarios. It does help in the development of aforementioned skills that pilots can use in such scenarios. Dynamic training is beneficial for aircrew, civilian operators and military mission training operations.
Modern flight training includes flight simulators built on high fidelity & high-quality modules like Presagis’ FlightSIM and HeliSIM solutions maximize efficient training with reduced costs and risks. The training curriculum includes various scenarios, maneuvers, emergency procedures, and so on. In certain cases, pilots might be underprepared to face critical never seen situations. But, with the skills gained from flight training, pilots are capable of handling real-world scenarios.
Let’s consider a slung load transport mission. Operating a helicopter in a hostile environment with a slung load is a tough task. With added interactions with ground control, other aircrafts and hostile forces, the pilot is in for a complex mission with rapid change of events. Training instructors and mission planners are required to replicate such dynamic scenarios with unexpected elements to prepare the pilot for scenarios that are beyond the operation of the aircraft.
To train the pilots in a flexible scenario environment, operators prefer using a representative aircraft simulation model and focus their resources on the design, execute and debrief customized training scenarios for the mission. A representative aircraft model will enable the pilot to focus on the successful mission completion without the distraction of low-quality aircraft models.
Creating a representative aircraft model is effectively done with subjective validation of the simulated aircraft and an experienced pilot. This method highlights specific aircraft behaviors and phenomena for the pilot to learn, recognize and anticipate. For example, with a conventional rotorcraft, pilots expect a decrease in the power required to hover in the proximity to the ground or flying through effective translational lift speed range produces a particular dynamic response. These cues are easily tuned, modeled, and simulated allowing pilots to focus on skill development.
Presagis provides easy-to-use and intuitive graphical user interface useable in multi-disciplinary aircraft design and modelling through FlightSIM and HeliSIM solutions. Users with full data or limited data access hold the provision to create high fidelity or representative aircraft models that can be customized and integrated into dynamic environments.
Applications of Presagis’ FlightSIM & HeliSIM solutions
Advanced technologies for flight simulation training has come a long way in the past decade. These simulators hold functionalities for different types of aircraft flights, cockpits and systems. Flight simulators enable users to easily configure the aircraft flight systems and dynamics with specifications such as rotor blade characteristics, aerodynamics coefficients, environmental parameters, ground interactions and more without any coding.
These solutions are an integral part of flight simulators for fixed wing and rotary wing used by both military and civil class aircrafts. The simulators are used as:
- Training devices for pilots and navigators
- Engineering test beds by R&D teams
- Air traffic management training devices
- Wargaming simulators of various degrees, simulate CI, C2, C4I systems etc. and more
Benefits of Presagis’ FlightSIM & HeliSIM solutions
- Intuitive UI for multi-disciplinary team: Easily simulate the flight models and systems using the enhanced user interface. Tools to view, compare, and modify your model without any coding.
- Flexible interface to add data packages in any format: Freedom to add data packages, regardless of the format with the solution interface.
- System simulations: Simulate and configure the Automatic Flight Control Systems (AFCS), gear box, radio navigation, and many more systems.
- Rapid Integration: Connect to any simulation framework out-of-the-box through CIGI, HLA and DIS. Easily integrate FSTD with third-party software as well.
- Slung load simulation model (with HeliSIM): Design, configure and hook up a load to the model. Configure the aerodynamic characteristics of the slung load.