An important success factor for farm equipment manufacturing companies is their ability to define and manufacture quality products tailored to customer preferences and deliver them anywhere in the world at record speed.
A farm equipment assembly can be very complex because it includes mechanical, electrical, hydraulic and pneumatic parts, sheet metal, cabling and automation mechanisms. Some 3D models can have more than 5,000 parts. It also consists of load-bearing frames that require structural analysis.
Need of the hour is to adopt the technology that uses single data driven approach, model-based product backbone that offers digital continuity and governance capabilities – from product engineering to manufacturing to service and maintenance – in one single repository to capitalize knowledge, intensify collaboration, improve productivity and stimulate innovation.
For some companies, digital transformation is a way to get closer to consumers, for others it means accelerating innovation or speeding time to market in order to stay closer to market trends. In any case, organizational process changes paired with modern technologies like PLM, Mobility, Cloud & SaaS can facilitate different ways of working.
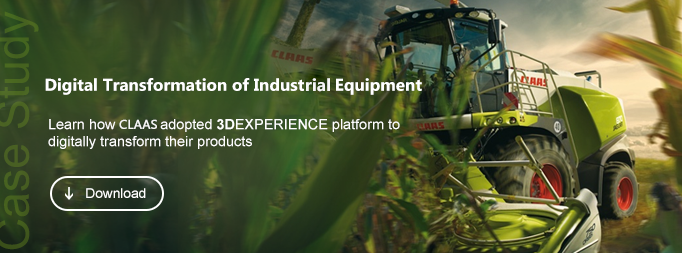
The 5 main compelling reasons to adopt digital transformation are:
-
- Quick Decision-Making and Risk Reduction
Today, organizations need to make quicker decisions and reduce risk at all times. It is important to implement a global, seamless governance also known as invisible governance to make sure all the administrative tasks are automated and transparent as much as possible. This will ensure faster, easier and safer decisions throughout the development cycle.
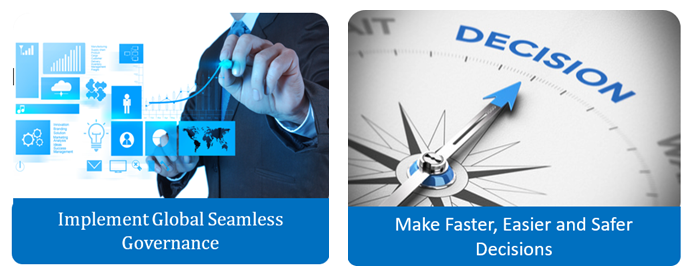
Organizations are able to plan ahead more easily and also departments can collaborate effectively with the R&D department thereby reducing errors significantly. This reinforces the importance of combining processes and technology to manage development scope, resources, and schedule. When a project is being planned, resources, schedule, and scope are often managed to ensure the current state is not in flux.
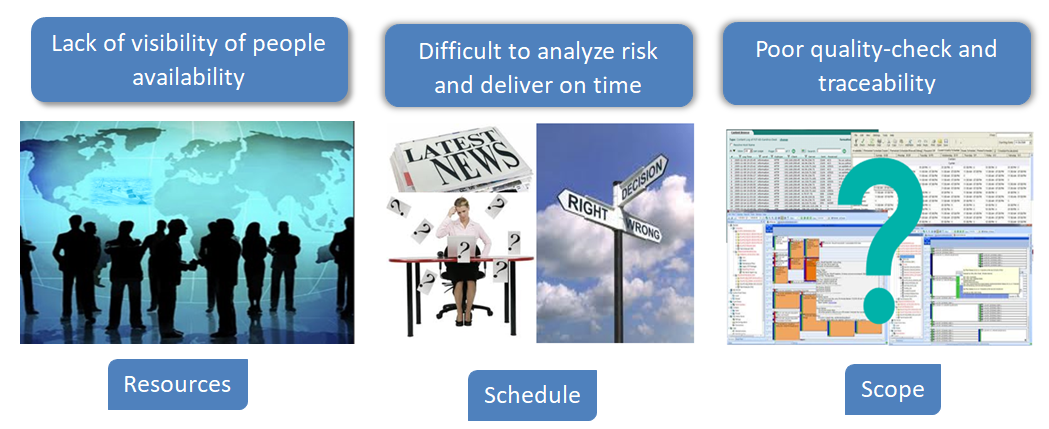
However, as the project proceeds, new information is gathered that causes adjustments to be made. Suddenly, having disconnected systems for scope, schedule or resources introduces uncertainty.
If a single technology is used to manage a project’s scope, schedule, and resources, then the risks associated with uncertainty are diminished or avoided entirely.
-
- Improve Engineering Productivity
To stay ahead of the latest innovations and market trends, companies must transition from traditional disconnected, discipline specific design and engineering bill of material processes to an approach that supports a single, fully consolidated approach. This helps in fully connected, global view of the combined product design structure and engineering bill of material with consistent global product development business processes.
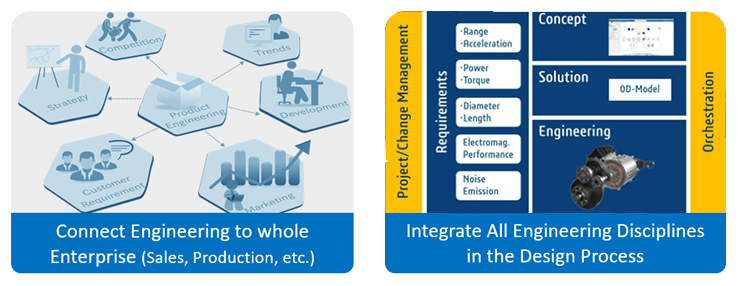
It is important to manage the engineering definition of products from early definition to final validation in collaboration across disciplines and the value network.
For this, all the engineering departments are required to be connected to the entire organization, sales, production, R&D, etc. Also, it is needed to integrate all the engineering disciplines in the design process seamlessly.
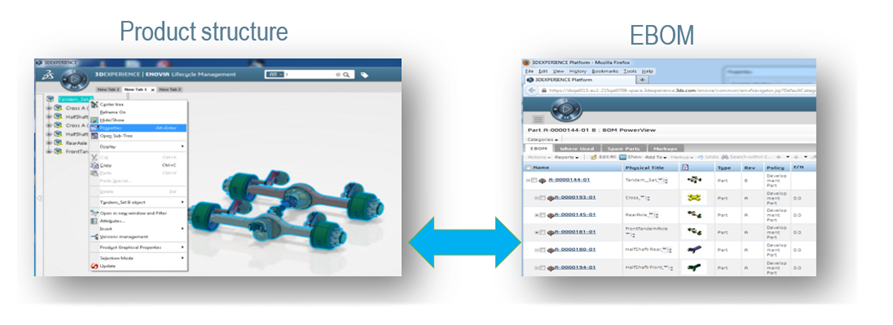
Adopting the digital continuity platforms allows process engineers to co-design the product with product engineers, check consistency of assemblies and improve the process and product quality.
-
- Improve Collaboration among Cross-Functional Teams – Bringing Teams Together
Working in silos between disciplines is a thing of the past. Digital team collaboration is a stimulus for innovation. Engineering teams need an essential set of tools for real-time, secure and structured collaboration on product content. Farm industry needs a scalable, online environment for managing product design, multi-physics simulation and manufacturing process planning with maximum traceability and flexibility.
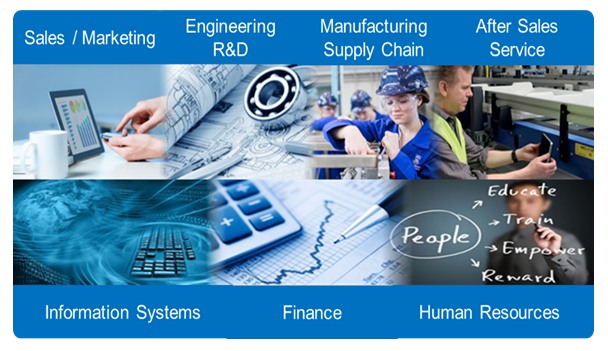
If the information is centrally managed and available to all stakeholders, it improves the competitiveness and resourcefulness to develop innovative products that rapidly respond to farmers’ evolving needs. Establishing a continuous digital thread across the entire product lifecycle empowers everyone to carry out their role to the best of their ability and build each machine first-time right.
-
- Enabling Validation through Virtual Twin
By modelling all the parts in 3D and then sharing this 3D model with the factory ensures accurate assembly of parts. In product architecture, it is possible to represent the kinematics assemblies. It enables to create mobile parts in 3D and make sure they do not interfere with other parts when the assembly is in action. This approach also helps the design team handle changes effectively and rectify errors quickly.
Thanks to virtual twin, the operators can easily understand assembly of new product variants and also get trained on new processes. It also enables plant managers to take right decisions regarding process schedule, material requirement and also plant maintenance. The customers can also view the products they ordered including all the various options even before it is produced.
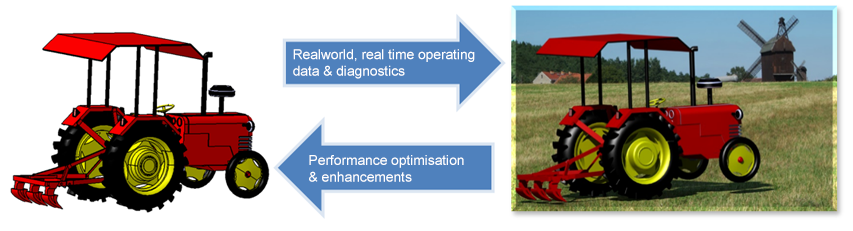
-
- Improving Understanding and Training of Workforce
Switching from 2D paper-based processes to 3D digital modelling has completely revolutionized the way today’s factory operators work. Previously, companies used to build a prototype assembly in a testing area to describe in 2D its assembly process, and sort this documentation in folders by product bill of materials. This 2D documentation was used for operator training and to update other operational documentation. Process updates were very complicated.

With digital tools adoption, it is easy to simulate assembly operations with overviews, and carry out assembly tests even before the receipt of parts and without any physical prototype. It has become far easier for companies to train their operators and prepare them to work on new models.
Today, with digital tools, we can run through the entire manufacturing process in detail, operators can be trained on the assembly processes before the product physically exists. When the operators visualize the product and factory model in 3D, they tend to quickly realize the new approach more clearly.
Adoption of digital transformation is a lot about a strong passion to innovate and excel in your area of work, leveraging exciting new tools to increase collaboration and above all delivering on the objective to serve the customer with the best products.